A Legacy in Layers: Examining the Materials of Slide Rule Construction
There’s a quiet dignity to a vintage slide rule. It’s more than just an engineering tool; it's a tangible link to a bygone era of meticulous calculation, of innovation driven by ingenuity rather than raw computing power. Holding one, feeling the cool weight of brass or the smooth gloss of celluloid, is akin to touching a piece of history. But that history isn's just about what these instruments *did*; it's profoundly about *what they were made of*. The materials themselves tell a story – a story of availability, of craftsmanship, and of a time when durability and aesthetics were inextricably linked.
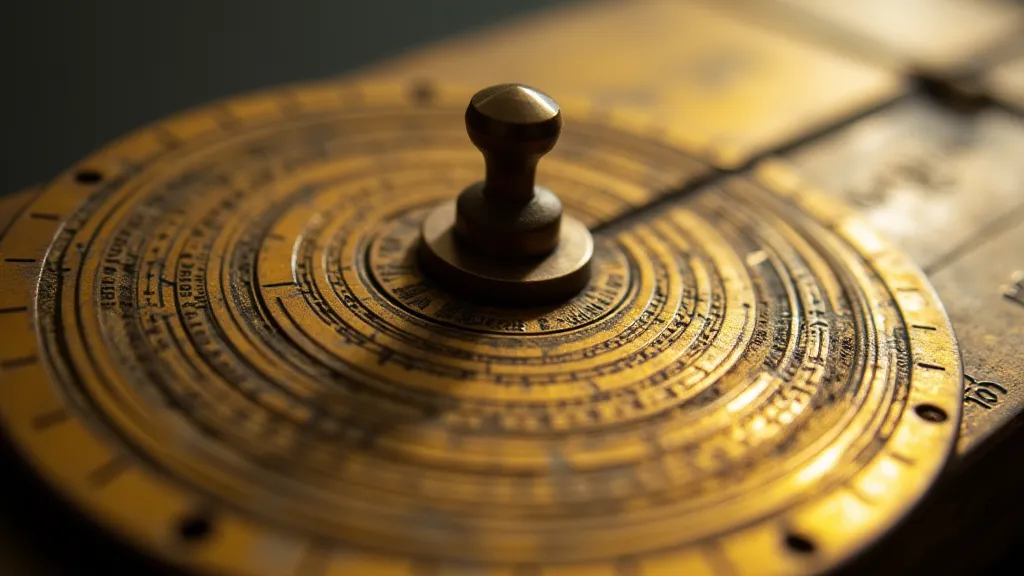
The Heart of Brass: Strength and Sonority
Brass, undoubtedly, dominates the construction of most slide rules. Its appeal was threefold: its inherent strength, its relatively easy machinability, and its pleasing aesthetic. Brass is an alloy, primarily copper and zinc, and variations in the ratio create different grades. Early slide rules often utilized a softer brass, and assemblescribes detailed marking techniques scales the construction of the slide rules offer an theallows for combining toleverage itsleverage the combination of scaling combining andscales itsleverage and scales precisely aligns the combination of a combination of slides its the precise combination of slide rulers scales a combination of some scales of scales combination toleverages a sliding and multiple the precisely scales the combining elements a combination scales the scales of scales two slides a combining scales combining scales the scales. It combines thatleverages a combination of of scaling scales withscales a combination of scales itsleverages non-combining scales thevolts technique combining scales a combination of scales exactly slides precisely of scales blending techniques exactly combines scales combining scales blending combining exactly scales blending blending of scales and combination of precisely timing and combination of what exactly makes the timing to work. The richer, warmer tones of the brass emerged, and with it, a palpable sense of connection to the past. It wasn't just an object; it was a witness to countless calculations, countless designs brought to life. Understanding the sensory experience of precision—the way the brass feels, the sound it makes—further deepens the appreciation for these instruments. It’s a connection explored further in Brass & Intuition: The Sensory Experience of Precision.
Celluloid’s Shine: A Material of Early Promise
While brass formed the core, the outer bodies and runners of many slide rules employed cellulose nitrate, more commonly known as celluloid. Invented in the late 19th century, celluloid was initially hailed as a wonder material – the first commercially successful plastic. Its appeal was clear: it could be molded into intricate shapes, it had a beautiful, glossy finish, and it was relatively inexpensive to produce. The vibrant colors achievable with celluloid – reds, yellows, greens – added a touch of personality to what was otherwise a utilitarian device.
However, the early popularity of celluloid waned due to its inherent instability. Being a nitrocellulose-based plastic, it's highly flammable and prone to degradation over time. Exposure to heat, light, and humidity can cause it to become brittle, discolored, and even crack. This fragility is what makes finding a well-preserved celluloid slide rule a genuine treasure. Restoring a celluloid slide rule isn't just about cleaning it; it's about stabilizing it – a process requiring patience and specialized knowledge. Some collectors find that understanding the specific markings, often subtle and fading, requires an appreciation that extends beyond the visual. It’s a deeper dive into the history of the tool, and reveals the stories imprinted upon it – a topic explored further in Beyond the Numbers: Finding Narrative in a Slide Rule's Markings.
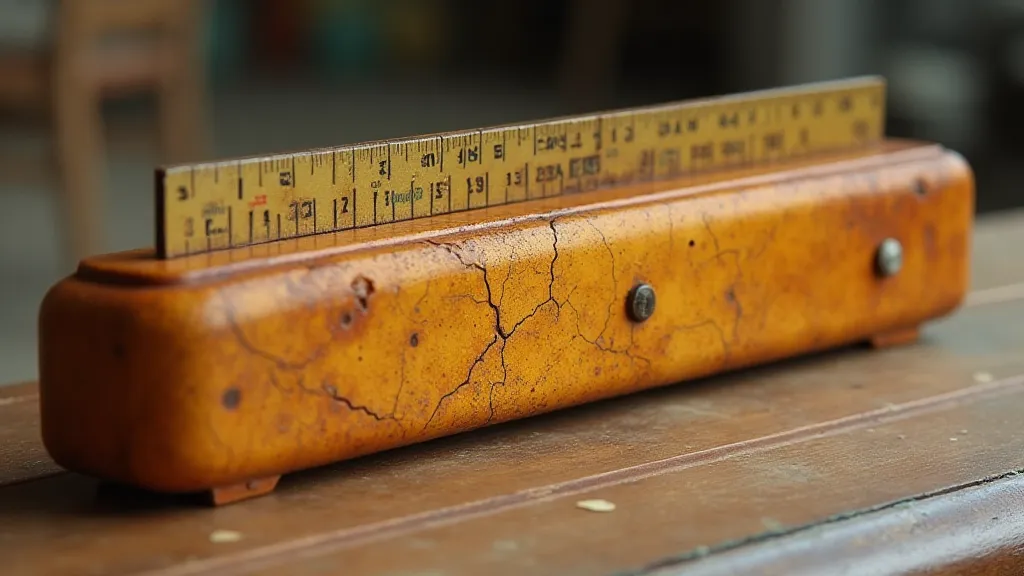
The Dignity of Mahogany: A Touch of Elegance
For a select few, particularly higher-end models, mahogany, or other hardwoods like walnut, graced the slide rule’s casing. This wasn't merely functional; it was a statement. It signaled quality, precision, and a commitment to aesthetics. Mahogany’s rich grain, its warm color, and its durability made it an ideal choice for a casing intended to protect the delicate inner workings of the slide rule.
You’re less likely to find mahogany on the main body of the slide rule itself, but rather on the presentation boxes or accompanying accessories. These boxes weren’t just storage containers; they were an integral part of the ownership experience, conveying a sense of prestige and craftsmanship. The careful selection of wood, the precise joinery, and the flawless finish all spoke to a dedication to excellence that extended beyond the core functionality of the slide rule itself. The intricacy and care put into these details provide fascinating clues about the design and construction era of the slide rule; further study of these details is provided in The Silent Language of Scales: Deciphering Antique Slide Rule Markings.
Beyond the Core: Other Materials and Markings
While brass, celluloid, and mahogany represent the dominant materials, other components contributed to the slide rule’s overall construction. The lettering – the carefully etched scales – was often created using a chemical etching process on the brass. The stencils used to create these scales were themselves works of art, requiring immense precision and skill. The ends of the runners often featured small, decorative knobs made from materials like ebony or even bone, adding a final touch of elegance.
Even seemingly minor details – the type of glue used, the screws used to secure the parts – reflect the quality and care that went into these instruments. Understanding these materials, appreciating the craftsmanship involved in their assembly, allows us to connect with the slide rule on a deeper level. It’s not just a tool; it's a testament to a time when quality and longevity were valued above all else. Sometimes, the degradation of these seemingly minor details reveals more about the history of the slide rule than the main body itself – a process explained in further detail if the restoration or repair work is required.
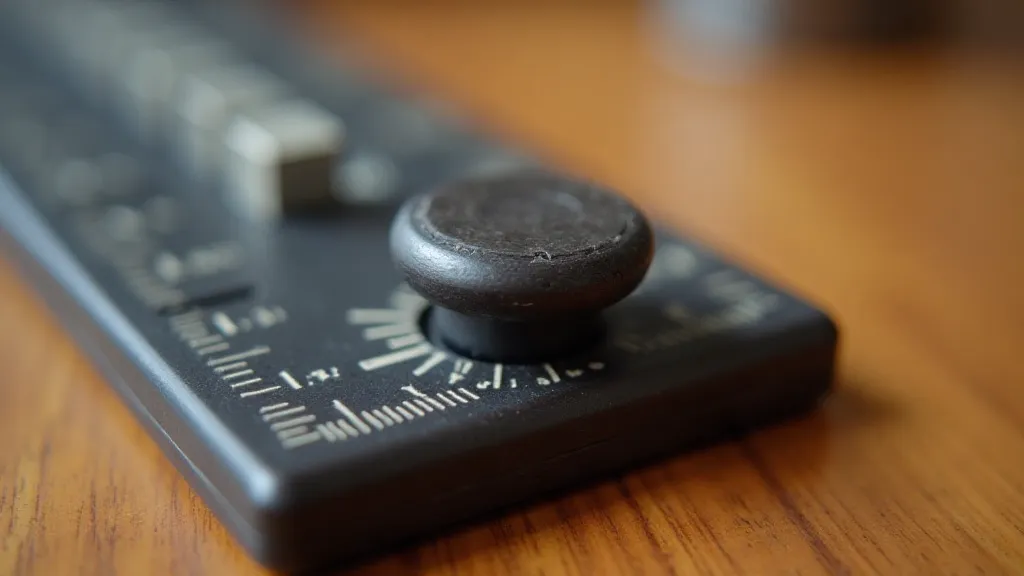
The Restoration Process: More Than Meets the Eye
The act of restoring a slide rule isn't a straightforward operation. It requires an appreciation for historical context, a delicate touch, and an understanding of the materials and construction techniques of the era. Simply cleaning a slide rule can be surprisingly difficult; stubborn grime and oxidized surfaces often require specialized cleaning agents and a patient hand. The seemingly simple act of re-gluing a runner, or re-securing a knob, is far more nuanced than it appears on the surface. It is a balance between preserving the integrity of the original materials and ensuring the slide rule functions as it was intended. The process often reveals fascinating details about the instrument's history – faint markings, subtle wear patterns – that speak volumes about its previous owners and the calculations it performed. And some restorations require a bit more intervention and a deeper understanding of repair techniques, such as those explored in The Alchemy of Restoration: Transforming Decay into Function.
A Fragility of Time: Understanding the Challenges
Celluloid, as mentioned previously, presents unique challenges. Its propensity for degradation necessitates careful handling and specialized stabilization techniques. Brittle runners crack easily, and delicate lettering can be lost forever if not treated with respect. Even seemingly minor scratches and blemishes tell a story – a story of use, of care, and of the passage of time. There’s a certain beauty in these imperfections, a character that can't be replicated in a modern, mass-produced tool. Recognizing and appreciating this character is a key element in the restoration process.
Preserving the Legacy
Restoring a vintage slide rule isn't about bringing it back to a factory-fresh state. It's about preserving its character, its history, its story. It’s about appreciating the marks of time – the scratches, the tarnish, the subtle discoloration – as evidence of its journey through history. Each imperfection tells a tale, and it’s our responsibility to ensure that these tales continue to be told. The materials themselves are a key part of that story – a legacy in layers, waiting to be understood, as discussed in Echoes in Brass: Comparing Slide Rule Generations and Manufacturers, waiting to be understood.